ٹھوسیت کے دوران گیس میں پھنسنے سے جوف کی قسم کی رکاوٹیں، MIG ویلڈنگ میں ایک عام لیکن بوجھل نقص ہے اور اس کی کئی وجوہات ہیں۔ یہ نیم خودکار یا روبوٹک ایپلی کیشنز میں ظاہر ہو سکتا ہے اور دونوں صورتوں میں اسے ہٹانے اور دوبارہ کام کرنے کی ضرورت ہوتی ہے - جس کی وجہ سے ٹائم ٹائم اور اخراجات میں اضافہ ہوتا ہے۔
سٹیل ویلڈنگ میں پورسٹی کی بڑی وجہ نائٹروجن (N2) ہے، جو ویلڈنگ پول میں شامل ہو جاتا ہے۔ جب مائع پول ٹھنڈا ہو جاتا ہے، تو N2 کی حل پذیری نمایاں طور پر کم ہو جاتی ہے اور N2 پگھلے ہوئے سٹیل سے نکل کر بلبلے (چھیدوں) کی شکل اختیار کر لیتا ہے۔ جستی/گیلوینیل ویلڈنگ میں، بخارات سے بنی زنک کو ویلڈنگ کے تالاب میں ہلایا جا سکتا ہے، اور اگر پول کے مضبوط ہونے سے پہلے فرار ہونے کے لیے کافی وقت نہیں ہے، تو یہ پورسٹی بناتا ہے۔ ایلومینیم ویلڈنگ کے لیے، تمام پورسٹی ہائیڈروجن (H2) کی وجہ سے ہوتی ہے، جس طرح N2 سٹیل میں کام کرتا ہے۔
ویلڈنگ کی پورسٹی بیرونی یا اندرونی طور پر ظاہر ہوسکتی ہے (اکثر ذیلی سطح کی پورسٹی کہلاتی ہے)۔ یہ ویلڈ پر یا پوری لمبائی کے ساتھ ایک نقطہ پر بھی ترقی کر سکتا ہے، جس کے نتیجے میں کمزور ویلڈ ہوتے ہیں۔
یہ جاننا کہ پوروسٹی کی کچھ اہم وجوہات کی شناخت کیسے کی جائے اور انہیں فوری طور پر کیسے حل کیا جائے معیار، پیداواریت اور نچلی لائن کو بہتر بنانے میں مدد مل سکتی ہے۔
ناقص شیلڈنگ گیس کوریج
ناقص شیلڈنگ گیس کوریج ویلڈنگ کی پورسٹی کی سب سے عام وجہ ہے، کیونکہ یہ وایمنڈلیی گیسوں (N2 اور H2) کو ویلڈ پول کو آلودہ کرنے دیتی ہے۔ مناسب کوریج کی کمی کئی وجوہات کی بناء پر ہو سکتی ہے، بشمول لیکن ان تک محدود نہیں، گیس کے بہاؤ کی خراب شرح، گیس چینل میں لیک ہونا، یا ویلڈ سیل میں ہوا کا بہت زیادہ بہاؤ۔ سفر کی رفتار جو بہت تیز ہے وہ بھی مجرم ہو سکتی ہے۔
اگر آپریٹر کو شبہ ہے کہ خراب بہاؤ مسئلہ کا سبب بن رہا ہے، تو اس بات کو یقینی بنانے کے لیے گیس کے فلو میٹر کو ایڈجسٹ کرنے کی کوشش کریں کہ شرح مناسب ہے۔ اسپرے ٹرانسفر موڈ استعمال کرتے وقت، مثال کے طور پر، 35 سے 50 کیوبک فٹ فی گھنٹہ (cfh) بہاؤ کافی ہونا چاہیے۔ زیادہ ایمپریجز پر ویلڈنگ کے لیے بہاؤ کی شرح میں اضافہ کی ضرورت ہوتی ہے، لیکن یہ ضروری ہے کہ شرح بہت زیادہ متعین نہ کی جائے۔ اس کے نتیجے میں بندوق کے کچھ ڈیزائنوں میں ہنگامہ آرائی ہو سکتی ہے جو شیلڈنگ گیس کوریج میں خلل ڈالتی ہے۔
یہ نوٹ کرنا ضروری ہے کہ مختلف طریقے سے ڈیزائن کی گئی بندوقوں میں گیس کے بہاؤ کی مختلف خصوصیات ہوتی ہیں (ذیل میں دو مثالیں دیکھیں)۔ اوپر والے ڈیزائن کے لیے گیس کے بہاؤ کی شرح کا "سویٹ اسپاٹ" نیچے والے ڈیزائن سے بہت بڑا ہے۔ یہ وہ چیز ہے جو ویلڈنگ انجینئر کو ویلڈ سیل لگاتے وقت غور کرنے کی ضرورت ہے۔
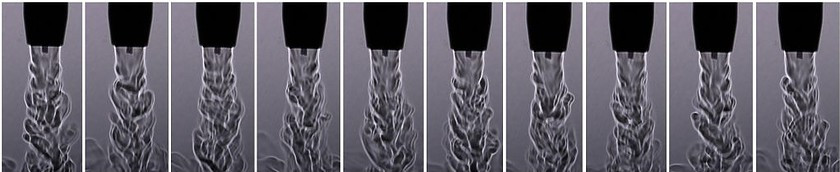
ڈیزائن 1 نوزل آؤٹ لیٹ پر ہموار گیس کے بہاؤ کو ظاہر کرتا ہے۔
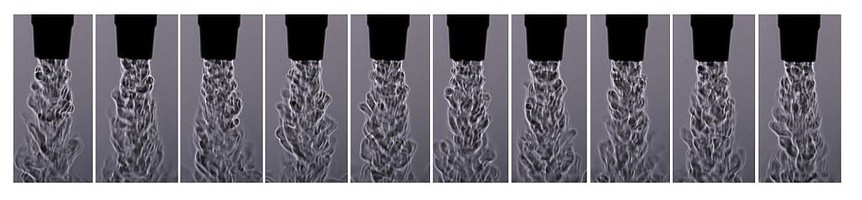
ڈیزائن 2 نوزل آؤٹ لیٹ پر ہنگامہ خیز گیس کے بہاؤ کو ظاہر کرتا ہے۔
MIG ویلڈنگ گن کے پاور پن پر گیس کی نلی، فٹنگز اور کنیکٹرز کے ساتھ ساتھ O-rings کو پہنچنے والے نقصان کو بھی چیک کریں۔ ضرورت کے مطابق تبدیل کریں۔
ویلڈ سیل میں آپریٹرز یا پرزوں کو ٹھنڈا کرنے کے لیے پنکھے کا استعمال کرتے وقت، اس بات کا خیال رکھیں کہ وہ براہ راست ویلڈنگ کے علاقے کی طرف اشارہ نہ کریں جہاں وہ گیس کی کوریج میں خلل ڈال سکتے ہیں۔ بیرونی ہوا کے بہاؤ سے بچانے کے لیے ویلڈ سیل میں اسکرین لگائیں۔
اس بات کو یقینی بنانے کے لیے روبوٹک ایپلی کیشنز میں پروگرام کو دوبارہ ٹچ کریں کہ کام سے کام کرنے کے لیے مناسب فاصلہ موجود ہے، جو کہ قوس کی مطلوبہ لمبائی کے لحاظ سے عام طور پر ½ سے 3/4 انچ ہوتا ہے۔
آخر میں، سست سفر کی رفتار اگر پورسٹی برقرار رہے یا بہتر گیس کوریج والے فرنٹ اینڈ پرزوں کے لیے MIG گن سپلائر سے مشورہ کریں۔
بنیادی دھاتی آلودگی
تیل اور چکنائی سے لے کر مل سکیل اور زنگ تک - بنیادی دھات کی آلودگی ایک اور وجہ ہے جو پوروسیٹی ہوتی ہے۔ نمی اس وقفے کو بھی حوصلہ دے سکتی ہے، خاص طور پر ایلومینیم ویلڈنگ میں۔ اس قسم کے آلودگی عام طور پر بیرونی پوروسیٹی کا باعث بنتی ہیں جو آپریٹر کو نظر آتی ہے۔ جستی سٹیل ذیلی سطح کی پورسٹی کا زیادہ شکار ہے۔
بیرونی پوروسیٹی کا مقابلہ کرنے کے لیے، ویلڈنگ سے پہلے بیس میٹریل کو اچھی طرح صاف کرنا یقینی بنائیں اور دھاتی کورڈ ویلڈنگ کی تار استعمال کرنے پر غور کریں۔ اس قسم کے تار میں ٹھوس تار کے مقابلے ڈی آکسیڈائزرز کی سطح زیادہ ہوتی ہے، اس لیے یہ بنیادی مواد پر باقی ماندہ آلودگیوں کو زیادہ برداشت کرتی ہے۔ ان اور دیگر تاروں کو ہمیشہ خشک، صاف ستھرا جگہ پر رکھیں جس کا درجہ حرارت پودے سے ملتا جلتا یا قدرے زیادہ ہو۔ ایسا کرنے سے گاڑھا پن کو کم کرنے میں مدد ملے گی جو ویلڈ پول میں نمی کو داخل کر سکتی ہے اور اس کا سبب بن سکتی ہے۔ تاروں کو ٹھنڈے گودام میں یا باہر ذخیرہ نہ کریں۔
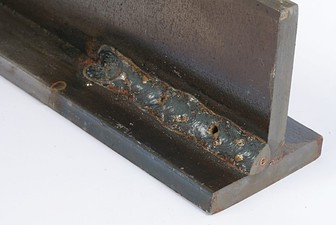
ٹھوسیت کے دوران گیس میں پھنسنے سے جوف کی قسم کی رکاوٹیں، MIG ویلڈنگ میں ایک عام لیکن بوجھل نقص ہے اور اس کی کئی وجوہات ہیں۔
جستی سٹیل کو ویلڈنگ کرتے وقت، زنک سٹیل کے پگھلنے سے کم درجہ حرارت پر بخارات بن جاتا ہے، اور تیز رفتار سفر ویلڈ پول کو جلدی منجمد کر دیتا ہے۔ یہ سٹیل میں زنک بخارات کو پھنس سکتا ہے، جس کے نتیجے میں پورسٹی ہوتی ہے۔ سفر کی رفتار کی نگرانی کرکے اس صورتحال کا مقابلہ کریں۔ ایک بار پھر، خاص طور پر ڈیزائن کردہ (فلوکس فارمولہ) دھاتی کورڈ تار پر غور کریں جو ویلڈنگ پول سے زنک بخارات کے فرار کو فروغ دیتا ہے۔
بھری ہوئی اور/یا کم سائز والی نوزلز
بھری ہوئی اور/یا چھوٹی نوزلز بھی پوروسیٹی کا سبب بن سکتی ہیں۔ ویلڈنگ کا چھڑکنا نوزل میں اور رابطہ ٹپ اور ڈفیوزر کی سطح پر جمع ہو سکتا ہے جس کی وجہ سے شیلڈنگ گیس کے بہاؤ کو محدود کیا جا سکتا ہے یا یہ ہنگامہ خیز ہو سکتا ہے۔ دونوں حالات ناکافی تحفظ کے ساتھ ویلڈ پول کو چھوڑ دیتے ہیں۔
اس صورت حال کو کمپاؤنڈ کرنا ایک نوزل ہے جو استعمال کے لیے بہت چھوٹا ہے اور زیادہ اور تیز اسپاٹر بنانے کا زیادہ خطرہ ہے۔ چھوٹے نوزلز بہتر مشترکہ رسائی فراہم کر سکتے ہیں، لیکن گیس کے بہاؤ کے لیے چھوٹے کراس سیکشنل ایریا کی وجہ سے گیس کے بہاؤ میں رکاوٹ بھی ڈال سکتے ہیں۔ ہمیشہ نوزل اسٹک آؤٹ (یا ریسیس) کے رابطے کے ٹپ کے متغیر کو ذہن میں رکھیں، کیونکہ یہ ایک اور عنصر ہوسکتا ہے جو آپ کے نوزل کے انتخاب کے ساتھ گیس کے بہاؤ اور پورسٹی کو متاثر کرتا ہے۔
اس بات کو ذہن میں رکھتے ہوئے، یقینی بنائیں کہ نوزل ایپلی کیشن کے لیے کافی بڑا ہے۔ عام طور پر، بڑے تار کے سائز کا استعمال کرتے ہوئے ہائی ویلڈنگ کرنٹ والی ایپلی کیشنز کو بڑے بور سائز کے ساتھ نوزل کی ضرورت ہوتی ہے۔
نیم خودکار ویلڈنگ ایپلی کیشنز میں، وقتاً فوقتاً نوزل میں ویلڈنگ اسپیٹر کو چیک کریں اور ویلڈر کے چمٹا (ویلپرز) کا استعمال کرتے ہوئے ہٹائیں یا اگر ضروری ہو تو نوزل کو تبدیل کریں۔ اس معائنہ کے دوران، تصدیق کریں کہ رابطہ ٹپ اچھی حالت میں ہے اور گیس ڈفیوزر میں واضح گیس پورٹس ہیں۔ آپریٹرز اینٹی اسپیٹر کمپاؤنڈ بھی استعمال کر سکتے ہیں، لیکن انہیں احتیاط کرنی چاہیے کہ نوزل کو کمپاؤنڈ میں بہت دور یا زیادہ دیر تک نہ ڈبوئیں، کیونکہ کمپاؤنڈ کی زیادہ مقدار شیلڈنگ گیس کو آلودہ کر سکتی ہے اور نوزل کی موصلیت کو نقصان پہنچا سکتی ہے۔
روبوٹک ویلڈنگ کے آپریشن میں، اسپاٹر کی تعمیر کا مقابلہ کرنے کے لیے نوزل کلیننگ اسٹیشن یا ریمر میں سرمایہ کاری کریں۔ یہ پیریفیرل پیداوار میں معمول کے وقفے کے دوران نوزل اور ڈفیوزر کو صاف کرتا ہے تاکہ یہ سائیکل کے وقت کو متاثر نہ کرے۔ نوزل کلیننگ سٹیشنوں کا مقصد اینٹی اسپیٹر سپرےر کے ساتھ مل کر کام کرنا ہے، جو کمپاؤنڈ کا ایک پتلا کوٹ سامنے والے اجزاء پر لگاتا ہے۔ بہت زیادہ یا بہت کم اینٹی اسپیٹر سیال اضافی پورسٹی کا نتیجہ بن سکتا ہے۔ نوزل کی صفائی کے عمل میں ہوا کے دھماکے کو شامل کرنے سے استعمال کی اشیاء سے ڈھیلے چھڑکنے کو صاف کرنے میں بھی مدد مل سکتی ہے۔
معیار اور پیداوری کو برقرار رکھنا
ویلڈنگ کے عمل کی نگرانی کرنے کے لیے احتیاط برتنے اور پوروسیٹی کی وجوہات جاننے سے، حل کو نافذ کرنا نسبتاً آسان ہے۔ ایسا کرنے سے زیادہ آرک آن ٹائم، کوالٹی کے نتائج اور پروڈکشن کے ذریعے زیادہ اچھے پرزے کو یقینی بنانے میں مدد مل سکتی ہے۔
پوسٹ ٹائم: فروری-02-2020