Xinfa ویلڈنگ کا سامان اعلی معیار اور کم قیمت کی خصوصیات ہے. تفصیلات کے لیے، براہ کرم ملاحظہ کریں:ویلڈنگ اور کٹنگ کے مینوفیکچررز - چین ویلڈنگ اور کٹنگ فیکٹری اور سپلائرز (xinfatools.com)
4. قوس کے گڑھے
یہ ویلڈ کے آخر میں نیچے کی طرف پھسلنے کا رجحان ہے، جو نہ صرف ویلڈ کی طاقت کو کمزور کرتا ہے، بلکہ ٹھنڈک کے عمل کے دوران دراڑیں بھی ڈالتا ہے۔
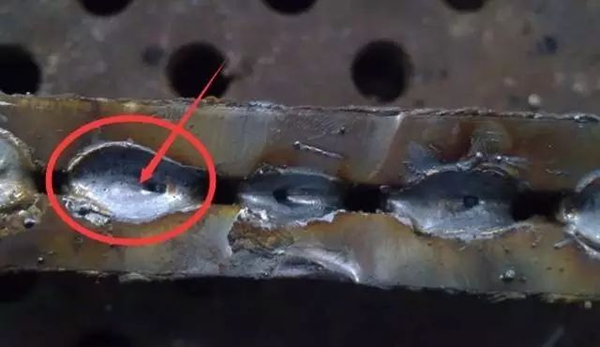
4.1 وجوہات:
بنیادی طور پر، ویلڈنگ کے اختتام پر آرک بجھانے کا وقت بہت کم ہوتا ہے، یا پتلی پلیٹوں کی ویلڈنگ کے وقت استعمال ہونے والا کرنٹ بہت بڑا ہوتا ہے۔
4.2 احتیاطی تدابیر:
جب ویلڈ ختم ہوجائے تو، الیکٹروڈ کو تھوڑی دیر کے لیے ٹھہرائیں یا کئی سرکلر حرکتیں کریں۔ آرک کو اچانک نہ روکیں تاکہ پگھلے ہوئے تالاب کو بھرنے کے لیے کافی دھات موجود ہو۔ ویلڈنگ کے دوران مناسب کرنٹ کو یقینی بنائیں۔ آرک پٹ کو ویلڈمنٹ سے باہر نکالنے کے لیے اہم اجزاء آرک اسٹارٹنگ پلیٹوں سے لیس ہوسکتے ہیں۔
5. سلیگ شامل کرنا
5.1 مظاہر: غیر دھاتی شمولیت جیسے کہ آکسائیڈز، نائٹرائڈز، سلفائیڈز، فاسفائیڈز وغیرہ غیر تباہ کن جانچ کے ذریعے ویلڈ میں پائے جاتے ہیں، مختلف قسم کی فاسد شکلیں بناتے ہیں، اور عام شکلیں شنک کی شکل، سوئی کی شکل اور دیگر ہوتی ہیں۔ سلیگ شمولیت دھاتی ویلڈز میں سلیگ کو شامل کرنا دھاتی ڈھانچے کی پلاسٹکٹی اور سختی کو کم کرے گا، اور تناؤ میں بھی اضافہ کرے گا، جس کے نتیجے میں ٹھنڈا اور گرم ٹوٹنا پیدا ہوتا ہے، جس سے اجزاء کو ٹوٹنا اور نقصان پہنچانا آسان ہے۔
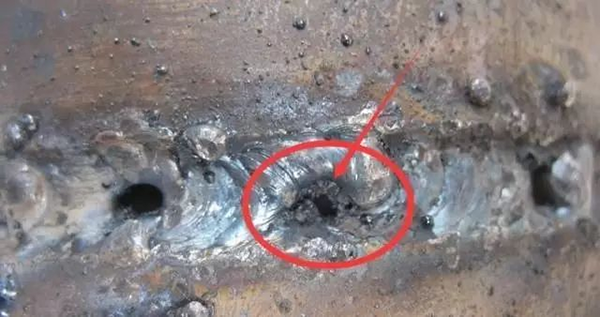
5.2 وجوہات:
5.2.1 ویلڈ بیس میٹل کو صحیح طریقے سے صاف نہیں کیا گیا ہے، ویلڈنگ کا کرنٹ بہت چھوٹا ہے، پگھلی ہوئی دھات بہت تیزی سے مضبوط ہو جاتی ہے، اور سلیگ کے پاس تیرنے کا وقت نہیں ہوتا ہے۔
5.2.2 ویلڈنگ بیس میٹل اور ویلڈنگ راڈ کی کیمیائی ساخت ناپاک ہے۔ اگر ویلڈنگ کے دوران پگھلے ہوئے تالاب میں آکسیجن، نائٹروجن، سلفر، فاسفورس، سلیکون وغیرہ جیسے متعدد اجزاء ہوں تو غیر دھاتی سلیگ آسانی سے بن جاتے ہیں۔
5.2.3 ویلڈر آپریشن میں ہنر مند نہیں ہے اور چھڑی کی نقل و حمل کا طریقہ غلط ہے، تاکہ سلیگ اور پگھلا ہوا لوہا آپس میں مل جائے اور الگ نہ ہو سکے، جو سلیگ کو تیرنے سے روکتا ہے۔
5.2.4 ویلڈ نالی کا زاویہ چھوٹا ہے، ویلڈنگ راڈ کی کوٹنگ ٹکڑوں میں گر جاتی ہے اور آرک سے نہیں پگھلتی ہے۔ ملٹی لیئر ویلڈنگ کے دوران، سلیگ کو صحیح طریقے سے صاف نہیں کیا جاتا، اور آپریشن کے دوران سلیگ کو بروقت نہیں ہٹایا جاتا، جو کہ سلیگ کو شامل کرنے کی تمام وجوہات ہیں۔
5.3 روک تھام اور کنٹرول کے اقدامات
5.3.1 صرف اچھی ویلڈنگ کے عمل کی کارکردگی کے ساتھ ویلڈنگ کی سلاخوں کا استعمال کریں، اور ویلڈڈ سٹیل کو ڈیزائن دستاویزات کی ضروریات کو پورا کرنا چاہیے۔
5.3.2 ویلڈنگ کے عمل کی تشخیص کے ذریعے معقول ویلڈنگ کے عمل کے پیرامیٹرز کا انتخاب کریں۔ ویلڈنگ کی نالی اور کنارے کی حد کی صفائی پر توجہ دیں۔ ویلڈنگ کی چھڑی کی نالی بہت چھوٹی نہیں ہونی چاہیے۔ ملٹی لیئر ویلڈز کے لیے، ویلڈز کی ہر پرت کے ویلڈنگ سلیگ کو احتیاط سے ہٹا دینا چاہیے۔
5.3.3 تیزابی الیکٹروڈ استعمال کرتے وقت، سلیگ پگھلے ہوئے تالاب کے پیچھے ہونا چاہیے؛ عمودی زاویہ سیون کو ویلڈ کرنے کے لیے الکلائن الیکٹروڈ کا استعمال کرتے وقت، ویلڈنگ کرنٹ کو صحیح طریقے سے منتخب کرنے کے علاوہ، مختصر آرک ویلڈنگ کا استعمال کرنا ضروری ہے۔ ایک ہی وقت میں، الیکٹروڈ کو مناسب طریقے سے جھولنے کے لیے الیکٹروڈ کو صحیح طریقے سے منتقل کیا جانا چاہیے تاکہ سلیگ سطح پر تیرنے لگے۔
5.3.4 ویلڈنگ سے پہلے پہلے سے گرم کریں، ویلڈنگ کے دوران گرم کریں، اور ویلڈنگ کے بعد موصلیت کا استعمال کریں تاکہ سلیگ کی شمولیت کو کم کرنے کے لیے اسے آہستہ آہستہ ٹھنڈا کریں۔
6. پوروسیٹی
6.1 مظاہر: ویلڈنگ کے عمل کے دوران پگھلی ہوئی ویلڈ میٹل میں جذب ہونے والی گیس کو ٹھنڈا ہونے سے پہلے پگھلے ہوئے تالاب سے خارج ہونے کا کوئی وقت نہیں ہوتا ہے، اور سوراخ کرنے کے لیے ویلڈ کے اندر ہی رہتی ہے۔ چھیدوں کے مقام کے مطابق، انہیں اندرونی اور بیرونی چھیدوں میں تقسیم کیا جا سکتا ہے۔ تاکنا کے نقائص کی تقسیم اور شکل کے مطابق، ویلڈ میں چھیدوں کی موجودگی ویلڈ کی طاقت کو کم کرے گی، اور تناؤ کا ارتکاز بھی پیدا کرے گی، کم درجہ حرارت کی ٹوٹ پھوٹ، تھرمل کریکنگ کا رجحان وغیرہ میں اضافہ کرے گی۔
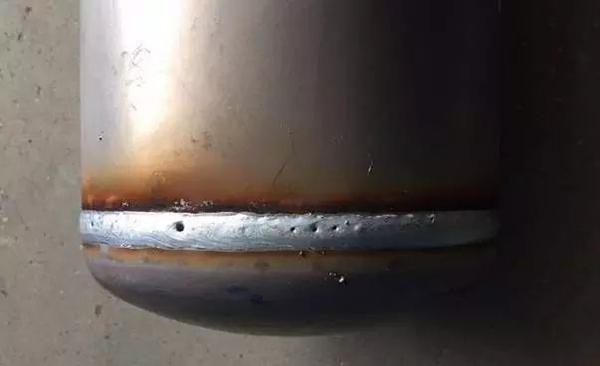
6.2 وجوہات
6.2.1 ویلڈنگ کی چھڑی کا معیار خود خراب ہے، ویلڈنگ کی چھڑی گیلی ہے اور مخصوص ضروریات کے مطابق خشک نہیں ہوئی ہے۔ ویلڈنگ راڈ کی کوٹنگ خراب ہو گئی ہے یا چھل گئی ہے؛ ویلڈنگ کور زنگ آلود ہے، وغیرہ۔
6.2.2 بنیادی مواد کو پگھلانے میں بقایا گیس ہے؛ ویلڈنگ کی چھڑی اور ویلڈمنٹ کو زنگ اور تیل جیسی نجاستوں سے داغ دیا جاتا ہے، اور ویلڈنگ کے عمل کے دوران، اعلی درجہ حرارت گیسیفیکیشن کی وجہ سے گیس پیدا ہوتی ہے۔
6.2.3 ویلڈر آپریشن ٹیکنالوجی میں ہنر مند نہیں ہے، یا اس کی نظر کمزور ہے اور وہ پگھلے ہوئے لوہے اور کوٹنگ میں فرق نہیں کر سکتا، تاکہ کوٹنگ میں گیس دھاتی محلول کے ساتھ مل جائے۔ ویلڈنگ کا کرنٹ بہت بڑا ہے، ویلڈنگ کی چھڑی کو سرخ کرتا ہے اور تحفظ کے اثر کو کم کرتا ہے۔ آرک کی لمبائی بہت لمبی ہے؛ پاور سپلائی وولٹیج میں بہت زیادہ اتار چڑھاؤ آتا ہے، جس کی وجہ سے آرک غیر مستحکم طور پر جل جاتا ہے، وغیرہ۔
6.3 روک تھام اور کنٹرول کے اقدامات
6.3.1 کوالیفائیڈ ویلڈنگ راڈز کا انتخاب کریں، اور پھٹے ہوئے، چھلکے ہوئے، بگڑے ہوئے، سنکی یا شدید زنگ آلود کوٹنگز کے ساتھ ویلڈنگ کی سلاخوں کا استعمال نہ کریں۔ ویلڈ کے قریب اور ویلڈنگ راڈ کی سطح پر تیل کے داغ اور زنگ کے دھبوں کو صاف کریں۔
6.3.2 مناسب کرنٹ کا انتخاب کریں اور ویلڈنگ کی رفتار کو کنٹرول کریں۔ ویلڈنگ سے پہلے ورک پیس کو پہلے سے گرم کریں۔ جب ویلڈنگ مکمل ہو جائے یا موقوف ہو جائے، تو قوس کو آہستہ آہستہ ہٹانا چاہیے، جو پگھلے ہوئے تالاب کی ٹھنڈک کی رفتار کو کم کرنے اور پگھلے ہوئے تالاب میں گیس کے اخراج کو کم کرنے کے لیے سازگار ہے، تاکنا کی خرابیوں کی موجودگی سے بچتا ہے۔
6.3.3 ویلڈنگ آپریشن سائٹ کی نمی کو کم کریں اور آپریٹنگ ماحول کے درجہ حرارت میں اضافہ کریں۔ باہر ویلڈنگ کرتے وقت، اگر ہوا کی رفتار 8m/s تک پہنچ جاتی ہے، بارش، اوس، برف وغیرہ، تو ویلڈنگ کے کاموں سے پہلے موثر اقدامات جیسے کہ ہوا کے ٹوٹنے اور چھتریوں کو اٹھانا چاہیے۔
7. ویلڈنگ کے بعد اسپیٹر اور ویلڈنگ سلیگ کو صاف کرنے میں ناکامی۔
7.1 رجحان: یہ سب سے عام عام مسئلہ ہے، جو نہ صرف بدصورت ہے بلکہ بہت نقصان دہ بھی ہے۔ فیوز ایبل اسپٹر مواد کی سطح کی سخت ساخت میں اضافہ کرے گا، اور سختی اور مقامی سنکنرن جیسے نقائص پیدا کرنا آسان ہے۔
7.2 وجوہات
7.2.1 ویلڈنگ کے مواد کی دوا کی جلد گیلی ہے اور اسٹوریج کے دوران خراب ہو جاتی ہے، یا منتخب کردہ ویلڈنگ راڈ بنیادی مواد سے میل نہیں کھاتا ہے۔
7.2.2 ویلڈنگ کے سازوسامان کا انتخاب ضروریات کو پورا نہیں کرتا، AC اور DC ویلڈنگ کا سامان ویلڈنگ کے مواد سے میل نہیں کھاتا، ویلڈنگ سیکنڈری لائن کا پولرٹی کنکشن کا طریقہ غلط ہے، ویلڈنگ کا کرنٹ بڑا ہے، ویلڈ نالی کا کنارہ ہے ملبے اور تیل کے داغوں سے آلودہ، اور ویلڈنگ کا ماحول ویلڈنگ کی ضروریات کو پورا نہیں کرتا۔
7.2.3 آپریٹر ہنر مند نہیں ہے اور قواعد و ضوابط کے مطابق کام اور حفاظت نہیں کرتا ہے۔
7.3 روک تھام اور کنٹرول کے اقدامات
7.3.1 ویلڈنگ کے بنیادی مواد کے مطابق مناسب ویلڈنگ کا سامان منتخب کریں۔
7.3.2 ویلڈنگ راڈ میں خشک کرنے اور درجہ حرارت کو برقرار رکھنے کا سامان ہونا چاہیے، اور خشک کرنے والے کمرے میں ایک ڈیہومیڈیفائر اور ایئر کنڈیشنر ہونا چاہیے، جو زمین اور دیوار سے 300 ملی میٹر سے کم نہ ہو۔ ویلڈنگ کی سلاخوں کو وصول کرنے، بھیجنے، استعمال کرنے اور رکھنے کے لیے ایک نظام قائم کریں (خاص طور پر دباؤ والے برتنوں کے لیے)۔
7.3.3 ملبے سے نمی، تیل کے داغ اور زنگ کو دور کرنے کے لیے ویلڈ کے کنارے کو صاف کریں۔ موسم سرما کے برسات کے موسم میں، ویلڈنگ کے ماحول کو یقینی بنانے کے لیے ایک حفاظتی شیڈ بنایا جاتا ہے۔
7.3.4 غیر الوہ دھاتوں اور سٹینلیس سٹیل کو ویلڈنگ کرنے سے پہلے، حفاظتی کوٹنگز کو ویلڈ کے دونوں اطراف کے بنیادی مواد پر تحفظ کے لیے لگایا جا سکتا ہے۔ آپ اسپٹر کو ختم کرنے اور سلیگ کو کم کرنے کے لیے ویلڈنگ کی سلاخوں، پتلی لیپت والی ویلڈنگ کی سلاخوں اور آرگن پروٹیکشن کا بھی انتخاب کر سکتے ہیں۔
7.3.5 ویلڈنگ آپریشن کے لیے ویلڈنگ سلیگ کی بروقت صفائی اور تحفظ کی ضرورت ہوتی ہے۔
8. قوس کا نشان
8.1 مظاہر: لاپرواہی سے کام کرنے کی وجہ سے، ویلڈنگ کی چھڑی یا ویلڈنگ ہینڈل ویلڈمنٹ سے رابطہ کرتا ہے، یا زمینی تار ورک پیس سے خراب رابطہ کرتا ہے، جس کی وجہ سے تھوڑی دیر کے لیے آرک بن جاتا ہے، جس سے ورک پیس کی سطح پر آرک کا داغ رہ جاتا ہے۔
8.2 وجہ: الیکٹرک ویلڈنگ آپریٹر لاپرواہ ہے اور حفاظتی اقدامات نہیں کرتا اور آلات کو برقرار نہیں رکھتا ہے۔
8.3 احتیاطی تدابیر: ویلڈرز کو باقاعدگی سے ویلڈنگ ہینڈل کے تار اور استعمال شدہ گراؤنڈ وائر کی موصلیت کی جانچ کرنی چاہیے، اور اگر وہ خراب ہو جائیں تو انہیں وقت پر لپیٹ دیں۔ زمینی تار کو مضبوطی اور قابل اعتماد طریقے سے نصب کیا جانا چاہیے۔ ویلڈنگ کرتے وقت ویلڈ کے باہر آرک شروع نہ کریں۔ ویلڈنگ کلیمپ کو بنیادی مواد سے الگ تھلگ رکھا جانا چاہئے یا مناسب طریقے سے لٹکایا جانا چاہئے۔ ویلڈنگ نہ کرنے پر بروقت بجلی کی سپلائی کاٹ دیں۔ اگر آرک پر خروںچ پائے جاتے ہیں، تو انہیں بروقت پیسنے والے پہیے سے پالش کرنا چاہیے۔ کیونکہ سنکنرن مزاحمت کی ضروریات جیسے سٹینلیس سٹیل کے ساتھ ورک پیس پر، آرک کے نشانات سنکنرن کا نقطہ آغاز بن جائیں گے اور مواد کی کارکردگی کو کم کر دیں گے۔
9. ویلڈ کے نشانات
9.1 رجحان: ویلڈنگ کے بعد ویلڈ کے نشانات کو صاف کرنے میں ناکامی آلات کے میکروسکوپک معیار کو متاثر کرے گی، اور غلط ہینڈلنگ بھی سطح پر دراڑیں ڈالے گی۔
9.2 وجہ: غیر معیاری آلات کی تیاری اور تنصیب کے دوران، پوزیشننگ ویلڈنگ فکسچر کی تکمیل کے بعد ان کو ہٹانے کی وجہ سے ہوتا ہے۔
9.3 احتیاطی تدابیر: اسمبلی کے عمل میں استعمال ہونے والے ہوسٹنگ فکسچر کو پیسنے والے پہیے سے پالش کیا جانا چاہیے تاکہ ہٹانے کے بعد بنیادی مواد سے فلش کیا جائے۔ بنیادی مواد کو نقصان پہنچانے سے بچنے کے لیے فکسچر کو دستک کرنے کے لیے سلیج ہیمر کا استعمال نہ کریں۔ الیکٹرک ویلڈنگ کے دوران آرک گڑھے اور خروںچ جو بہت گہرے ہوتے ہیں ان کی مرمت اور پیسنے والے پہیے سے پالش کی جانی چاہیے تاکہ پیرنٹ میٹریل سے فلش کیا جا سکے۔ جب تک آپ آپریشن کے دوران توجہ دیتے ہیں، اس خرابی کو ختم کیا جا سکتا ہے.
10. نامکمل دخول
10.1 رجحان: ویلڈنگ کے دوران، ویلڈ کی جڑ مکمل طور پر پیرنٹ میٹریل یا پیرنٹ میٹریل کے ساتھ فیوز نہیں ہوتی ہے اور پیرنٹ میٹریل کو جزوی طور پر نامکمل طور پر ویلڈ کیا جاتا ہے۔ اس نقص کو نامکمل دخول یا نامکمل فیوژن کہا جاتا ہے۔ یہ جوڑوں کی مکینیکل خصوصیات کو کم کر دیتا ہے اور اس علاقے میں تناؤ کا ارتکاز اور دراڑوں کا سبب بنے گا۔ ویلڈنگ میں، کسی بھی ویلڈ کو نامکمل دخول کی اجازت نہیں ہے۔
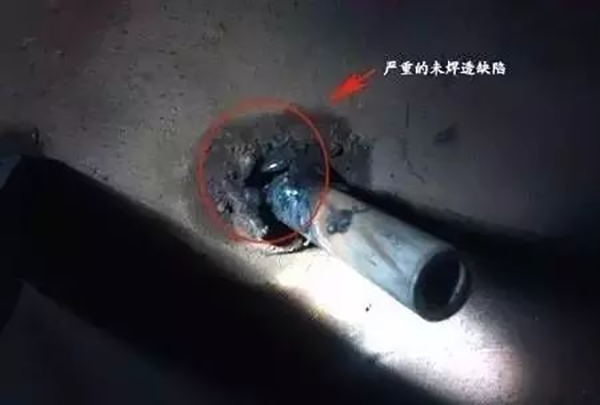
10.2 وجوہات
10.2.1 ضوابط کے مطابق نالی پر کارروائی نہیں کی جاتی ہے، کند کنارے کی موٹائی بہت بڑی ہے، اور نالی کا زاویہ یا اسمبلی کا خلا بہت چھوٹا ہے۔
10.2.2 جب دو طرفہ ویلڈنگ کی جاتی ہے تو پچھلی جڑ کو اچھی طرح سے صاف نہیں کیا جاتا ہے یا نالی کے اطراف اور انٹرلیئر ویلڈ کو صاف نہیں کیا جاتا ہے، تاکہ آکسائیڈ، سلیگ وغیرہ دھاتوں کے درمیان مکمل فیوژن میں رکاوٹ بنیں۔
10.2.3 ویلڈر آپریشن میں ہنر مند نہیں ہے۔ مثال کے طور پر، جب ویلڈنگ کا کرنٹ بہت بڑا ہوتا ہے، تو بنیادی مواد پگھلا نہیں ہوتا، لیکن ویلڈنگ کی چھڑی پگھل جاتی ہے، تاکہ بیس میٹریل اور ویلڈنگ کی چھڑی جمع شدہ دھات ایک ساتھ نہ ملیں۔ جب کرنٹ بہت چھوٹا ہو؛ ویلڈنگ راڈ کی رفتار بہت تیز ہے، بنیادی مواد اور ویلڈنگ کی چھڑی جمع شدہ دھات اچھی طرح سے نہیں مل سکتی؛ آپریشن میں، ویلڈنگ راڈ کا زاویہ غلط ہے، پگھلنا ایک طرف متعصب ہے، یا ویلڈنگ کے دوران پھونکنے کا واقعہ پیش آئے گا، جو نامکمل دخول کا سبب بنے گا جہاں آرک کام نہیں کر سکتا۔
10.3 احتیاطی تدابیر
10.3.1 ڈیزائن ڈرائنگ یا تصریح کے معیار میں بیان کردہ نالی کے سائز کے مطابق گیپ کو پراسیس کریں اور اسمبل کریں۔
پوسٹ ٹائم: جولائی 28-2024